Factory-made furniture is to interior design what fast food is to dining. Without a doubt, it has several pluses: It’s quick, readily available at a variety of locations, reasonably priced and usually consistent in quality. But the things that make “fast furniture” appealing to many people make it undesirable or unsuitable to others. The more you shop for furniture-especially if you have a specific need-the more you begin to doubt those “selling points” of mass-produced factory furniture. It’s available quickly, but what good is speed if you can’t find an armoire deep enough to hold your video equipment? It’s also available at many locations-which means that an exciting shopping trip can get boring very quickly as you begin to see the same piece at store after store. And even though the quality is generally consistent, especially within a particular line, that quality may not be up to your standards. Solid wood furniture with no particleboard, for example, is virtually impossible to find in “fast furniture.” Many people are more concerned with how something looks than how it’s made. Unfortunately, they often pay in the long run when they buy factory pieces that don’t last or wear well. Even the consistency can be maddening if you’re looking for an unusually long table to fit against a long wall. Standard sizes that can’t be altered are a fact of life with factory furniture. Once you’ve shopped around and have become familiar with 1983 prices, you may realize that you’ve been fooling yourself by thinking that factory furniture was reasonably priced, especially considering the quality. Being able to note the difference in good, better and best is the cutting edge between quickness and quality. And in few areas other than custom furniture can that difference be so readily discerned. Many people admit that they can’t tell the difference between a high-end factory piece and its custom counterpart, which is nothing to be ashamed of. It merely goes to show that handcrafted furniture isn’t everyone’s priority, desire or need. Several lines of good factory furniture exist, so why would anyone want a handcrafted piece?
“Why buy a Rolex watch instead of a gold-plated Timex?” craftsman Richard Wincorn asks. “Both keep time; in fact, the Timex may even do it a little better. It [the Rolex] is a luxury that someone wants.”
“Why” can go beyond pure luxury to specific needs. A handcrafted piece can add an embellishment or important detail.
Some other reasons to consider hand-crafted furniture:
Scale. “Different size people want different size sofas,” says Mark Busboom of R.T. Mark and Associates. Handmade furniture isn’t confined to the limits of set factory dimensions, so if your 6-foot-4-inch husband wants a sofa he can stretch out on, a piece can be designed just to fit him.
Construction. Most factory pieces are glued together, which often results in the loosening of joints. Handcrafted furniture also may be glued together. However, Wincorn secures many of the glued places with small pegs to prevent shifting.
The term “handcrafted” connotes that most things are done by the hands of skilled craftsmen. Of course, some things are done better by modern-day means; staple guns hold a sofa skirt more securely than the old hand-hammered tacks.
“We have to be more precise,” says Ron Grazier. “We won’t accept anything but quality. A lot of cabinet shops settle for ’good enough’ and think the trim people or painters will cover up [a mistake].”
Finish. “The finish can ruin a beautiful piece of furniture or make a plain piece beautiful,” Grazier says. Most furniture makers say that finishing a piece takes as long as its actual construction.
“The first thing a person does to a piece of handcrafted furniture is to put his hand on it,” Wincorn says. “They don’t do that with a factory piece; they’ll stand back and look at it. There’s a warmth about a handmade piece. I don’t know what makes it so unless people sense the time and effort involved.”
Of the various finishes available, lacquer is one of the most popular now, but it seems to be controversial within the trade. While it gives a more natural-looking finish of hand-rubbed wood, some craftsmen avoid it for lack of durability, saying that it won’t last for more than a year without scratching.
Rocky Gregory of European Custom Furniture Design Company and Harry Parker of Harry Parker and Associates use acrylic urethane (more commonly known as automotive finish since it’s used on jets and diesel trucks) instead of lacquer. Gregory says the finish is five times harder than lacquer and that scratches can be easily buffed out. It gives a highly polished, modern, almost hi-tech look.
“Finishes are our forte,” says Busboom. R.T. Mark offers finishes to look like such things as lacquered grass cloth, leather, parchment, brass, stainless-steel inlays – even goatskins and kilim rugs.
IN ADDITION to the ever-increasing number of Dallas furniture stores (not to mention the showrooms at the World Trade Center), Dallas has a group of highly skilled furniture craftsmen who not only build to specifications, but who use techniques that most people thought had died with the industrial Revolution.
Who are the people who create these works of art? Solitary craftsmen hammering away in dark, dusty workrooms? Not quite. While settings vary from Parker’s bare-bones shop in a metal warehouse to Manheim’s elegant showroom, only in Parker’s case did we find the “solitary workman.” Wincorn has one employee; Manheim has six; Gregor, 12; and R.T. Mark, 30.
“There’s a lot of false conceptions of ’the solitary craftsman working alone,’ ” says Gregor. “Most pieces we see from the past were made by a craftsman surrounded by many people. He never worked alone. In those days and today, the work was attributed to one person, even though there was a ’school’ [of students] around him. To be ’of the school’ doesn’t say the master did it nor does it imply that he didn’t do it. ’Ye little old craftsman’ never amounts to much, in my opinion. It’s the vibration a group gets when we consult constantly with each other.”
On the other hand, Wincorn, an architect by training, prefers to keep his hands dirty and work in his small shop. “I like to be involved in the process myself. When I’m not involved, the work changes and the quality suffers a little. If I’m not looking at everything, I start letting things slide – and that’s not healthy for business.”
Handcrafting furniture is often considered a dying art. Qualified craftsmen are hard to find and even harder to keep. European-trained artists serve a long apprenticeship, something that ambitious young American craftsmen find unappealing.
When Manheim Galleries opened its custom-furniture shop, owner Edward Weitz did so because of his cabinetmaker and his carver. “These two are the top people in the world. Without them, I wouldn’t have even considered doing this,” he says.
Since these people are artists, designers, craftsmen and perfectionists, there is usually nothing they can’t build. The only limitation for most craftsmen is cost -and that is more of a limitation to the client than to the craftsman.
“The most fascinating thing [about the business] is figuring out what a person wants and then making it just for him,” Parker says. “Meeting someone’s true desire, need and fantasy with something- that means more to me than any check that could be written. And you know when you do it.”
Some unusual pieces have been designed and crafted in these studios. Jim Morris of Century Glass Inc. of Dallas has constructed a glass-top occasional table to encase and follow the lines of an elephant’s ear. He has also made and installed a floor-to-ceiling free-standing beveled glass shower stall. Busboom designed a sectional sofa for a yacht that had to fit through a 24-inch porthole before being assembled inside the boat. The lines of the sofa back had to follow the gently sloping lines of the boat.
Besides occasional whim pieces, most furniture builders receive orders for traditional pieces such as tables (occasional, coffee, end and dining), mantels, desks, breakfront cabinets, chairs and bedroom pieces. Armoires are often custom-built to house entertainment centers that require a deeper-than-average cabinet.
MANY PEOPLE would never consider handcrafted furniture because of what they assume to be its high cost. While it is difficult for furniture makers to compete with factory prices, their prices are frequently comparable to the high end of manufacturers’ prices.
Booth believes that custom furniture doesn’t have to be expensive. His craftsmen have built dining tables for $1,500, coffee tables for $400 to $600 and mantels for $500 to $600.
Gregor agrees. “We can adapt to the amount of money to be spent without compromising on the line. One dining-room table may cost $15,000 and another $900, and both may have the same quality of line and the same silhouette, but there’s a variation in detail, carving, patina or wood. Two things can vary in price from $300 to $1,500 without arguing that one is good or one is bad.”
One potential drawback of custom furniture is its lack of a money-back guarantee. As the client, you are consulted throughout the designing for your ideas and approval; many shops encourage customers to come in during the construction to watch the progress. Therefore, the final result is generally considered to be the client’s responsibility.
Construction time for most handmade furniture varies from 10 to 12 days to four months; 60 days is about average. If there is a holdup in the order, it is usually after the design is done when the customer is trying to make up his mind whether that is what he wants. “People tend to hem and haw around, then they want it yesterday,” Morris says. “They really don’t want us to rush, though. This is a work of art for the amount of labor that goes into it.”
Most furniture craftsmen advertise only in the Yellow Pages, if at all. They depend on customer referrals and on inquiries about their pieces. Some of them deal only with architects and interior designers; others deal directly with clients.
Most furniture makers consider the Dallas market very traditional. Wincorn says that when the Dallas market wants contemporary pieces, people choose metal and glass rather than wood. Parker has found this attitude very frustrating. “I brought some striking but not radical [contemporary] things to Dallas, and peo-ple didn’t understand them.” He enjoys working with rare or tropical woods, which he says the Dallas market is hesitant to accept.
FINDING A furniture maker with whom you can work will require some interviewing on your part. If you’re working with a designer, all three personalities must mesh. As Gregor explains, “The chemistry between the client, designer, me, my people-even my suppliers-is quite important, and that’s a lot of chemistry.”
Remember that there may be no money-back guarantee, but your satisfaction is of the utmost importance. Each piece of furniture is a part of the person who built it, and there’s an intense pride in workman-ship not often found today. At Booth Galleries, for example, craftsmen handcarve the gallery’s signature into each piece. “We think we’re making the antiques of today,” Booth says.
Wincorn echoes that feeling: “I want the things I make to be things [my clients] can give their children.”
Booth Galleries, 2121 McKinney Ave. 742-8760.
Century Glass Inc. of Dallas, 1417 N. Washington. 823-7773.
European Custom Furniture Design Company, 4305 W. Lovers Lane. 352-6270.
Ron L. Grazier Inc., 1110 Summit #9, Piano. 867-8991.
Gregor Studios, 3315 McKinney Ave. 528-0870.
Manheim Galleries, 2520 Fairmount. 742-2364.
R.T. Mark and Associates Inc., 1718 HiLine Drive. 748-7693.
Harry Parker & Associates, 2351 Merrell Road. 241-4397.
Richard Wincorn Studio Inc., 10118Cayuga. 328-6826.
Get our weekly recap
Brings new meaning to the phrase Sunday Funday. No spam, ever.
Related Articles
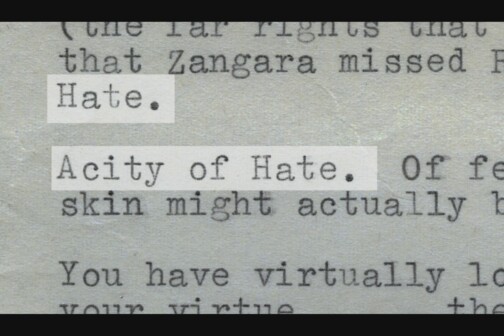
Arts & Entertainment
DIFF Documentary City of Hate Reframes JFK’s Assassination Alongside Modern Dallas
Documentarian Quin Mathews revisited the topic in the wake of a number of tragedies that shared North Texas as their center.
By Austin Zook
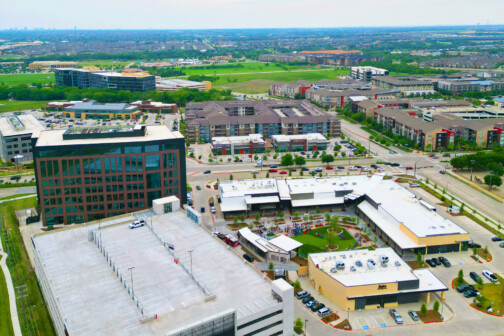
Business
How Plug and Play in Frisco and McKinney Is Connecting DFW to a Global Innovation Circuit
The global innovation platform headquartered in Silicon Valley has launched accelerator programs in North Texas focused on sports tech, fintech and AI.
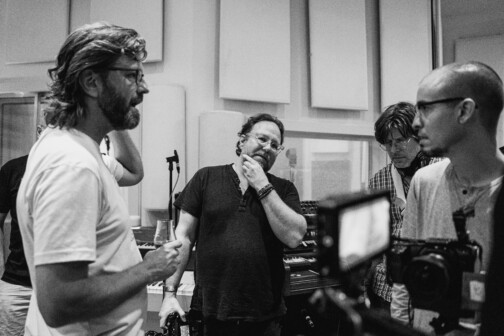
Arts & Entertainment
‘The Trouble is You Think You Have Time’: Paul Levatino on Bastards of Soul
A Q&A with the music-industry veteran and first-time feature director about his new documentary and the loss of a friend.
By Zac Crain