Architects understand the cost of hiring a value engineer who skimps on the details. Finding one who has the perfect equilibrium between design savvy, cost-effectiveness, and the leadership mojo that inspires teams to meet deadlines—that’s almost a luxury.
So, when luxury firms hire civil engineers for office remodeling, they tend to look for the best.
Tyton Holdings joined the Dallas investment scene in 2021, making waves in multiple industries thanks to its innovative approaches to acquisitions and growth. Founded in 2011, Tyton provides its steadily expanding ranks of affiliate companies with a powerful model for investment funding. The company’s recipe for internally sourced capital simultaneously drives up the bottom line within Tyton’s portfolio while also giving its managers comfortable autonomy.
As a majority owner and operator for a portfolio spanning oil and gas, construction and engineering, mitigation and restoration, government services, and more, Tyton has established its holding periods with a mid-to-long-term strategic outlook. When its portfolio expanded to encompass new markets, its investors sought a fresh, central location for its headquarters so they could manage relationships with stakeholders from the Gulf Coast to the Permian Basin. As was the case for many businesses in recent years, Dallas became Tyton’s perfect fit.
When Tyton relocated from Denver, its entire suite of affiliate companies needed a space that fit its vast array of objectives. Nestled in a bustling commercial nexus within Dallas-Fort Worth, the 52,000-square-foot Addison Airport complex was a prime location. It was an optimal hub for Tyton affiliates with Dallas-based business operations. It offered ample space to house the group’s corporate air transportation, keeping executives a short hop from their entire national network of companies.
But while the facility had the right amount of space, it needed substantial renovations to serve Tyton’s purposes. Although the airport offices had recently undergone major modeling upgrades, they didn’t have the kind of open design that would allow a multi-industry conglomerate to house its national operations center. Tyton needed space for business leaders in distinct industries to operate independently. It needed a centralized communications nerve center. It needed just a touch of luxury appropriate to its brand. And it needed to accomplish all of this with economical and precise engineering. Enter Aislan Toshinaga.
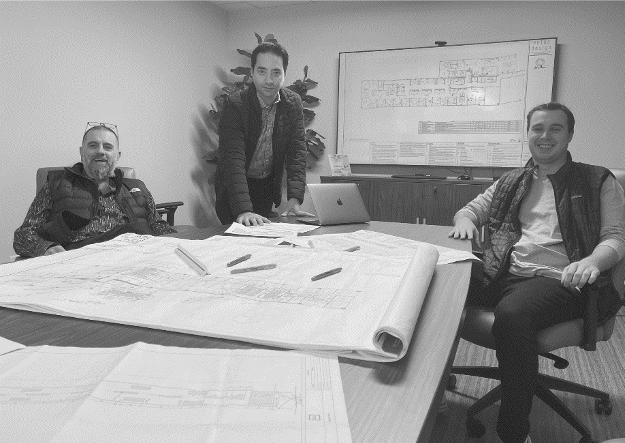
Toshinaga is a Brazilian engineer and construction project manager with a storied reputation for business growth in his industry. Serving in key roles at the Kauffman Group and Lock Engenharia, two of the most reputable engineering companies in Brazil, Toshinaga was known for innovating designs and work approaches that combined the academic attunement of a master’s degree in engineering with a keen eye for budget.
During his years with the Kauffman Group, Toshinaga rose to prominence in high-end construction through his work on a renowned luxury coffee farm. Here, he developed a cost-saving rain shelter over the construction site using existing materials, streamlining the budget, and avoiding weather delays that would have otherwise capsized the project’s timeline. His creative eye and financially conscious planning earned him a reputation with the project architect, the legendary Joao Mansur, who soon regarded Toshinaga as one of his most sought-after engineering specialists and project directors.
Toshinaga’s reputation attracted luxury clients around the world. He went on to work on projects such as Louis Vuitton’s first Veuve Clicquot retail space in South America, amplifying an already powerful organization’s performance in a new market through brilliant execution of the architect’s design.
This required a human touch. As a manager, Toshinaga was known for his ability to assemble the troops, developing a tight community of vendors and contractors who regularly went the extra mile on projects.
By connecting with teams in the trenches, he was able to cultivate a loyalty that inspired collaborative efforts seldom seen in construction: Material sellers pulled extra strings to get rarer, luxury flooring tiles, circumventing supply chain delays. Electricians stayed after hours to waterproof systems if the weather called for flooding. Toshinaga was a rallying point for participants and stakeholders, thanks to an approachable management style and an ability to facilitate solutions.
Tyton’s Headquarters: Melding Architectural Vision with Engineering Economy
Initially hired as a project manager for a disaster restoration firm that Tyton had acquired, Toshinaga was called upon for his rare combination of entrepreneurial and civil engineering expertise. His knowledge base in multifamily housing also allowed Tyton’s affiliate to expand its offerings in reconstruction.
Because of the time-essential nature of developing Tyton’s corporate epicenter, along with the significance of aesthetics in luxury branding, Toshinaga was the ideal choice for an investment group that wanted to display high-grade visual elegance throughout its offices.
“The main goal for any project is to ensure that the building owner’s vision is translated properly into architectural design,” Toshinaga says. “It’s the project manager’s responsibility to take that vision into account while giving valuable engineering options to lower costs for the owner.”
For Tyton, this meant use of space was of prime importance—offices needed to be functional for hosting business leaders in multiple industries, allowing for both independent function and frequent collaboration. Toshinaga helped Tyton integrate cost and function in areas like electrical engineering and sound control.
“For example, the architect’s original design for the renovated space called for acoustic beams,” he says. This was a costly expense, where other materials could have served the same purpose equally well. “Instead, we advocated for aluminum beam ceilings. These saved an overwhelming 50 percent in costs for that portion of the design without sacrificing acoustic quality or aesthetics.”
A Multi-Industry Communications Mecca
Construction also needed to consider the operational demands of sophisticated technology—including massive computing power, nationwide logistical management systems, and sufficient lighting for the space.
“We wanted to implement designs and layouts in a way that made sense from an engineering standpoint,” Toshinaga says. “This meant taking MEP (mechanical, electrical, and plumbing) into consideration, along with its impact on the visual design.”
To put it simply, the pipes can’t occupy the same space as the power cables. Navigating the labyrinth of a building’s mechanical and electrical infrastructure is often a main contributor to an overextended budget. The more sophisticated the power situation becomes, the more likely a project runs into supply chain issues—especially when aesthetics comes into play. This necessitates value engineering—the science and art of finding a realistic workaround within time constraints without sacrificing quality.
“Lighting was one of the big aesthetic elements of the space at Tyton,” he says. “We were able to match the architect’s design for color tone, light level requirements, and also respect electrical code specifications. And we did it while using value engineering principles to save 70 percent on the originally budgeted costs in lighting.”
Luxury On the Mind
Other areas where Toshinaga faced supply chain delays include flooring and the door panels, two of the most immediately noticeable visual elements in the space. Although vendors received clearly delineated expectations for materials, COVID-induced backups demanded rapid adaptation. Thanks to some quick thinking, Toshinaga was able to identify alternative materials and source them in time to meet project deadlines.
“It’s hard to put a value on a good relationship with vendors,” he says. “This allows me to get things done earlier. For example, a few weeks ago, we were putting the finishing touches on Tyton’s corporate office, and that included bringing in a firm from California to install a golf simulator. When they were beginning the installation, we found a sprinkler line that was in the way of the wiring for the simulator’s cameras. Thankfully, we had the foresight to anticipate that issue. I had already talked to my fire sprinkler contractor about the possibility, and we were able to plan his schedule so that he could be available to work with the simulator installation team to troubleshoot the issue.”
It was an apt consideration on the part of Toshinaga and his team. Having a contractor on call did cost a little—but a delay in installation would have cost the client up to $5,000. It’s this kind of planning that luxury brands look for in value engineering.
The Tyton Holdings corporate office begins full-scale operations in January 2023.
With the successful completion of the Tyton Holdings headquarters, Aislan Toshinaga has been hired as Tyton’s on-staff senior project manager for construction endeavors and will oversee projects for its entire list of subsidiaries. His scholarly work has been published at Mackenzie Presbyterian University in São Paulo. Toshinaga’s engineering designs and operational strategies are still in regular commercial use in Brazil more than one decade after their initial deployment.
Author
